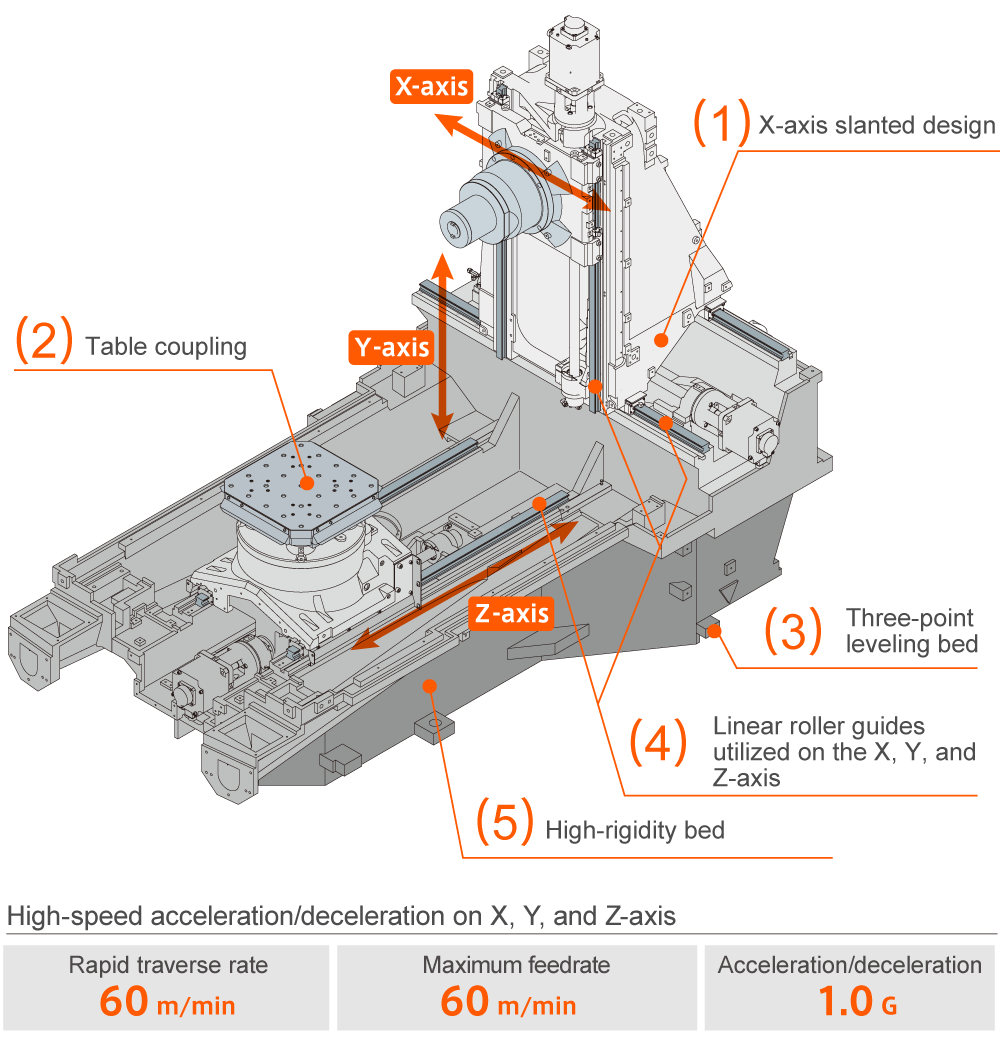
(1) X-axis slanted design
The mounting surfaces of the X-axis linear guide rails are at different heights to ensure high rigidity for high-speed and high-accuracy positioning.
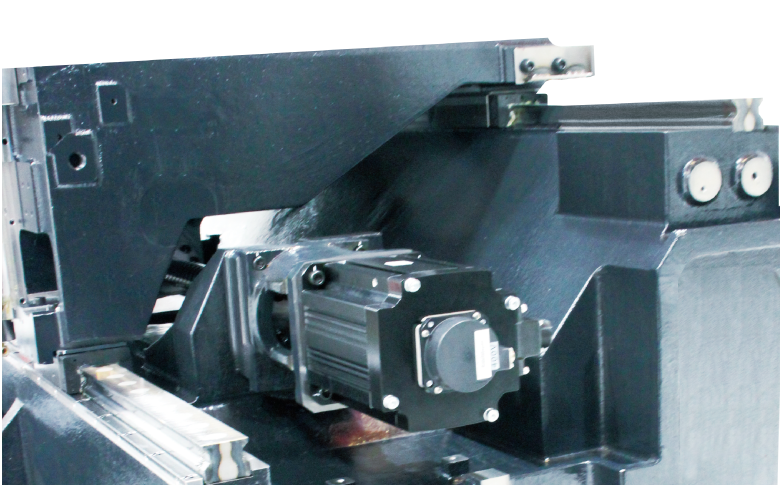
(2) Table clump
The table and pallet are clamped on 4 taper cones for stable heavy-duty machining.
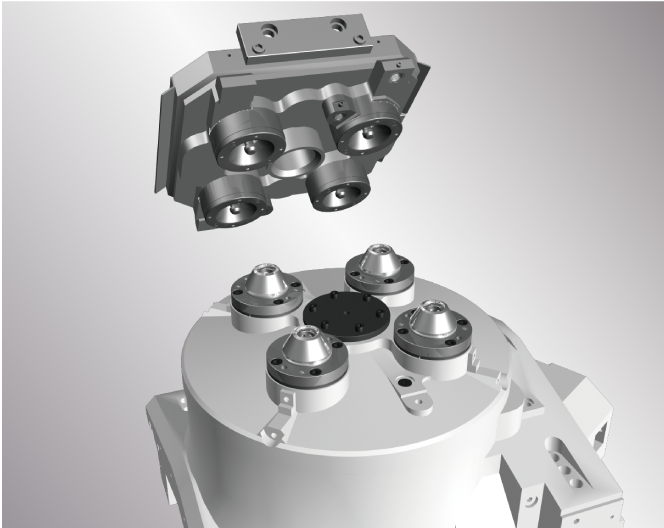
(3) Three-point leveling bed
Three-point leveling bed simplifies machine installation.
(4) Linear roller guides utilized on the X, Y, and Z-axis
The HCN series uses linear roller guides on the X, Y, and Z-axis for high-accuracy and heavy-duty machining.
(5) High-rigidity bed
The high-rigidity bed is reinforced with strategically located ribs to ensure stability during X and Z-axis travel.
Spindle
Integral spindle/motor
The integral spindle/motor design minimizes vibration during high-speed operation to ensure exceptional surface finishes and maximize tool life.
Spindle thermal control
For high-accuracy machining, temperature-controlled cooling oil circulates around the spindle bearings and headstock to minimize any thermal change to the spindle.
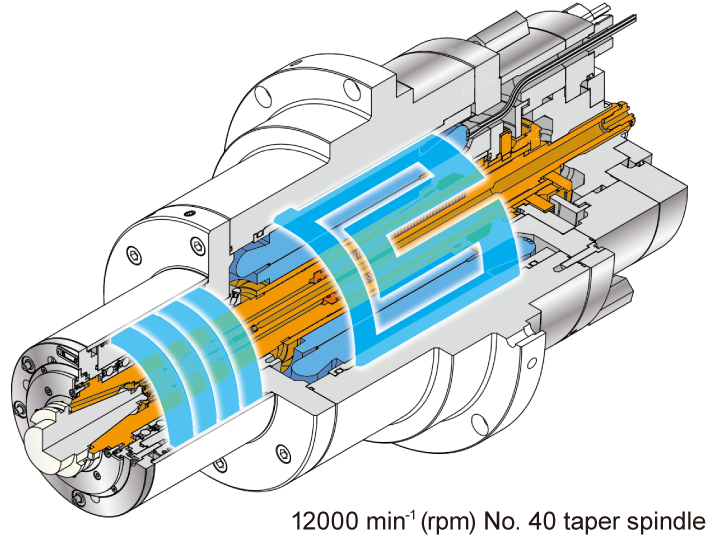
Spindle variation
Standard [ 12000 min-1(rpm) ] *
Speed | 12000 min-1(rpm) | |
---|---|---|
Output | 18.5 kW (25 HP) [40% ED] | |
15 kW (20 HP) [cont. rating] | ||
Max. torque | 81.9 N・m [40% ED] |
* Standard spindle varies depending on the region.
High torque [ 15000 min-1(rpm) ] (OPTION)
Speed | 15000 min-1(rpm) | |
---|---|---|
Output | 46 kW (62 HP) [40% ED] | |
37 kW (50 HP) [cont. rating] | ||
Max. torque | 200 N・m [40% ED] |
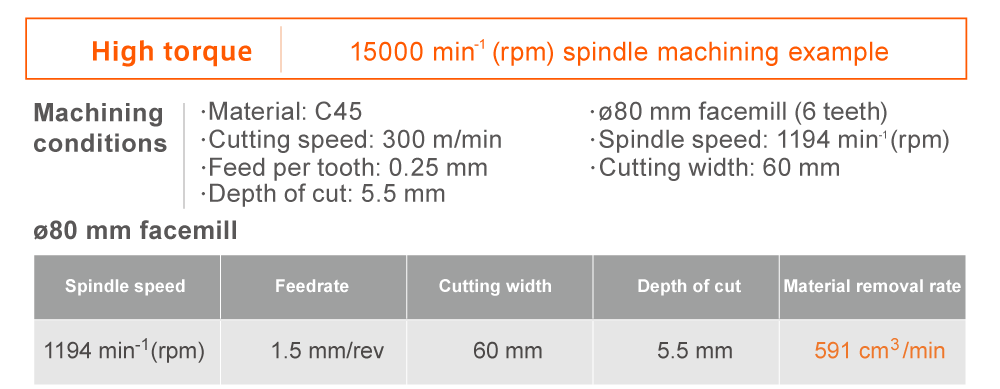
High speed [ 18000 min-1(rpm) ] (OPTION)
Speed | 18000 min-1(rpm) | |
---|---|---|
Output | 35 kW (47 HP) [40% ED] | |
26 kW (35 HP) [cont. rating] | ||
Max. torque | 84 N・m [40% ED] |
High speed, high output [ 20000 min-1(rpm) ] (OPTION)
Speed | 20000 min-1(rpm) | |
---|---|---|
Output | 42 kW (56 HP) [40% ED] | |
26 kW (35 HP) [cont. rating] | ||
Max. torque | 161 N・m [40% ED] |
High speed [ 25000 min-1(rpm) ] (OPTION)
Speed | 25000 min-1(rpm) | |
---|---|---|
Output | 23 kW (31 HP) [40% ED] | |
15 kW (20 HP) [cont. rating] | ||
Max. torque | 22 N・m [40% ED] |